A New Year's Resolution Suggestion For The FDA
By Mike Levitt, senior industry observer
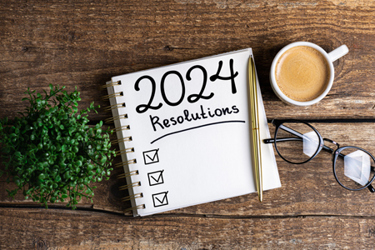
This is the time of the year when, after enjoying the holidays, many of us are doing our best to implement and maintain the resolutions we made for the new year. Some of us look to be healthier, spend more time with the family, reduce stress, or make a greater contribution to our companies or communities.
Over the last couple of years, many of my colleagues and I have written about the continuing compliance problems identified during inspections by our friends at the FDA and how the nature of these deficiencies hasn’t changed in the last 20-plus years (see “A Discourse on Pharmaceutical cGMP FDA Form 483 Trends,” by Steven J. Lynn, American Pharmaceutical Review, May/June 2022). We also know that, as good auditors, FDA investigators identify priority areas for review in their inspections and can have themes that they follow for a specific inspection cycle based on the previous year’s inspection findings. We also know that the old military adage “respect what is inspected” is how the pharma industry decides how to invest resources. This is evident in how the industry has responded in recent years to the agency’s focus on data integrity, implementing programs and spending millions of dollars on consultants and seminars.
So, to the management leadership in the FDA, as you prepare for 2024, I would like you to consider a New Year’s resolution to focus a significant portion of your site inspections on the effectiveness of training and education of the manufacturing workforce. My suggestion is based on the belief that the true root cause of many of the deficiencies identified each year, whether it is poor investigations, data integrity, inadequate quality oversight, or many others routinely identified, is the lack of an effective program to ensure personnel have been properly educated and trained to do their jobs. For my industry colleagues, consider the list below as the foundation for sustainable quality in an increasingly complex manufacturing landscape.
Please look beyond training records, resumes, and deviations. I would suggest the following areas for inspection and evaluation:
- Is there a dedicated training group with the experience and credentials to teach others?
- Is the training and education effort only focused on new hires and changes in procedures or is there understanding of the need for ongoing training to ensure competence?
- If subject matter experts provide the training, are they given enough time to perform these tasks and be educated on how best to deliver the knowledge required in addition to their full-time jobs?
- Are there well-defined curricula and course packages that ensure the needed skills are provided, including why tasks should be performed in a certain way?
- Are the number of courses in the curricula reasonable to allow completion in a timely fashion and allow refresher training on a regular basis?
- Is there an annual training plan and calendar that defines the time to be devoted to training and education and is there a metric that measures compliance with the calendar?
- In interviews with operational personnel, can they explain how they keep up to date with changes or new procedures and stay effective on existing processes?
As 2024 begins, we are still dealing with the effects of the pandemic, workforce shortages, and rapid changes and growth in many facets of pharmaceutical and biopharmaceutical manufacturing. To quote David Mierau in the November/December 2022 issue of Contract Manufacturing, “sustainable manufacturing, once seen as a “nice to have,” today is a business imperative. The path to more sustainable operations is paved with technology, but starts with people.” I agree with David and believe that the foundation must be built on properly training and educating our workforce. So, I ask my colleagues in the FDA to resolve to make 2024 a year that focuses at least a part of their investigational effort on this fundamental process to ensure compliance and sustainable quality.
About The Author:
Mike Levitt is a veteran operations senior executive with more than 47 years in the pharmaceutical industry with companies like Eli Lilly, Solvay, and entrepreneurial biotech operations. Prior to his retirement from consulting with Quality Executive Partners (QxP) at the end of November 2023, as the senior VP of strategic development, he coached and mentored the company’s senior leadership to improve leadership skills and develop appropriate strategies.