Developing Life Sciences Real Estate At The Speed Of Innovation
By Ken Richter and Jeff Janicek
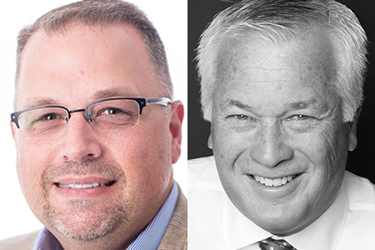
Speed always has been a hallmark of the life sciences sector, with first movers standing to gain considerable market share while delivering much-needed medical devices and pharmaceuticals to the public.
But the race to produce a COVID-19 vaccine and related therapies is unlike anything that has come before, with a dozen potential vaccines already entering Phase 3 clinical trials only months after the virus was identified.
While we don’t know exactly when a COVID-19 vaccine will be widely available, research and development has advanced to combat this global threat at a pace that can only be described as “breakneck.” In contrast to today’s day-to-day progress, the mumps vaccine — considered the fastest ever approved — took four years to advance from collecting viral samples to administering a licensed drug.
Hopefully, COVID-19 is a once-in-a-lifetime event, and there won’t be a need for a worldwide, all-hands-on-deck effort in the future. But the lessons the life sciences space is learning now about fostering innovation, creating efficiencies, and coordinating activities across research, development, manufacturing, and distribution will shape the industry in the years to come.
Those lessons inevitably include new thinking about the space where life science work happens, especially in R&D labs that are the origins for so much of today’s groundbreaking discoveries, but also in administrative and other services that support this work. Any real estate decision made today will have real-world implications for years to come, so it’s imperative that companies get it right and meet the demand for prescription drugs, personalized medicine, gene therapies, and other emerging solutions.
The Changing Nature of Life Sciences Innovation
Life sciences companies look different today than they have in years past, when massive pharmaceutical companies and smaller, more nimble biotechnology firms dominated the space. Today, much of the innovation is driven by venture-capital-backed startups, which don’t have the operating capital to build expansive corporate campuses and purpose-built labs.
These companies graduate from shared incubators to leased lab space, often in life sciences hubs like Boston, San Francisco, and San Diego where academics, research institutions, and talent pools coexist. While every lab has its own sophisticated needs, there are enough commonalities that existing lab space can be modified and generally repurposed as companies evolve and expand.
One of the downsides of this concentration of life science innovators is available lab space is leased quickly in today’s market. Life sciences companies tend to group together, whether in city centers or suburban hubs, and while companies can and do lease space that is further removed from existing clusters, it can be difficult to attract the talent that is so vital to driving innovation if the research facility isn’t in the right area.
Even when lab space is available, companies must be diligent in determining whether the existing space can support their work. A former biological lab is more easily converted to new biological efforts, rather than reworking the space for chemistry, for instance. And just as innovation has accelerated new solutions for the public, the methods that drive lab work also have evolved, with new equipment and research approaches dictating how the space is conceptualized.
Redeveloping Alternative Property Types
Given the competitive landscape of existing lab space, earlier-stage life sciences companies may initially land in buildings not necessarily designed for lab work. While labs carry special requirements not common in other development types — including greater ceiling heights, unique lab equipment, more robust HVAC systems, and structural considerations — developers are increasingly trying to lure life sciences companies that want to remain in high-demand areas without building from the ground up and look to these repositioned building alternatives.
While the prospect of redeveloping an existing building in a life science sub-market — such as an industrial warehouse or manufacturing facility — is achievable, the challenges associated with fitting out these buildings for the specific requirements of lab work can be complex and costly and require thorough due diligence. These properties, meanwhile, aren’t just there for the taking. Quality industrial and manufacturing buildings are in high demand as a result of changing consumer habits, which have been shifted by COVID-19.
The repurposed universe consists almost entirely of steel and concrete structures. Wooden structures are often the cheapest to lease or develop but they don’t offer the inherent requirements for chemical control zones and other protections of more robustly built properties. Attempting to retrofit a wooden structure to support lab science work has inherent limitations, which developers should take into account.
Managing High-Cost Items
The most expensive and unique aspect of a lab build-out are the mechanical, electrical, and plumbing (MEP) systems, which, along with lab benching, push the project cost into the hundreds of dollars per square foot, even when the space meets other structural and space considerations.
These expenses affect the entire development, not just the lab space. A tenant with an equal split between lab and administrative workers may desire typical office amenities: high, open ceilings and ample free space. Similar to the technology-based offices of today, these features come at a premium and will likely be separated from the laboratories.
MEP and equipment considerations aren’t exclusive to redeveloping non-life sciences buildings either, as existing systems in former labs may be outdated and not easily adaptable. These often end up on the scrap pile, replaced with modern equipment in a similar process to bringing in new MEP systems to former warehouses or manufacturing facilities. However, second- or even third-generation lab buildings typically have the structural, ceiling height, and routing of the MEP systems considerations already deployed.
Additionally, not all labs serve the same purpose; some special lab equipment will require unique customization of the space, which must be identified and incorporated early in the design process. Buying only the equipment that is needed can save money up-front and over the long term. Unnecessary lab equipment comes with a high energy draw and heat load output, both of which can contribute to unnecessary costs for years to come.
Today’s labs are run differently than those of decades past: There is a stronger connection between time spent in the lab, related office or computer activities, and collaborating with coworkers. This significant change in work patterns calls for streamlined workflow and a more efficiently designed space that naturally supports the different types of work being performed. A better flow between the lab space and office space can increase productivity as well as optimize usable square feet — and rent.
Best Practices for Embarking on New Real Estate Projects
As long as speed is a factor in life science development success, expanding lab space will be an important consideration for many companies. Though the development and redevelopment process is costly and complex, it doesn’t have to distract from the essential business of creating life-saving and enhancing breakthroughs.
Taking a creative, practical, and flexible approach to building out lab space can help life sciences companies compete, both now and well into the future.
# # #
Ken Richter is Western regional president and head of the life sciences practice for, Project Management Advisors, Inc., a national real estate advisory firm.
Jeff Janicek, VP, Skender, has 30 years of construction experience and currently leads the firm’s healthcare and lab sciences construction teams, based in Chicago.