Essential Medicines And The Need For A Robust U.S. Supply Chain
By Dave Stowe
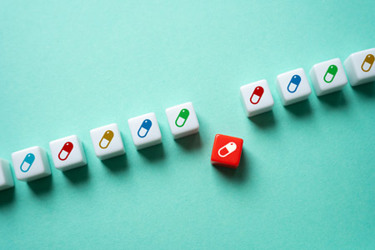
Essential medicines play a vital role in America’s health, and the supply is closely monitored by the FDA and industry groups. These medicines sustain life, provide life support and/or the prevention of debilitating diseases. The inability to supply these medicines to the market adversely impacts patients and their families’ lives. Currently, there are 227 essential medicines across all dosage forms which face a risk of supply shortage.
Between 2017 and 2023, new drug shortages in the U.S. rose by 38%, averaging a 5% annual increase. Ongoing drug shortages surged by 139% over the same period, growing at an average rate of 16% per year. Further, shortages of essential medicines last almost twice as long (4.0 years) as non-essential medicines (2.3 years).
Currently, only 12% of active pharmaceutical ingredients (APIs) are produced in the U.S., while India, the EU, and China dominate global API production, supplying 75% of the U.S. market. Of the global facilities approved for API production, just 4% are in the U.S. For finished dosage forms, the U.S. produces 37% of its own supply, with India, the EU, and China accounting for 50%. Further complicating the situation are recent U.S. tariffs on the importation of all goods.
Despite efforts from manufacturers, healthcare providers, patient advocacy groups, and government agencies to address these shortages, U.S. manufacturing capabilities remain severely limited, hindering progress.
Path Forward
Given the current situation, growing the U.S. manufacturing base will require a collaborative framework between industry, academia, government regulators and politicians. A combination of continued private and public investment will be needed to manage global risk, improve manufacturing capability and target government support.
Globalization Risk
While global supply chains have provided lower costs and innovation, there are several risks facing producers and regulators that are changing the value of global sourcing. These risks include export regulations, U.S. tariffs, longer inspection times for compliance of foreign facilities, logistics risks, and an inability to quickly respond to demand and inventory loss.
Historically, the primary reason to offshore manufacturing was cost, rather than a value-driven decision. While American manufacturing often is considered “high cost,” companies and investors should evaluate their cost drivers given the improving capabilities in manufacturing technology, quality management, and supplier capabilities. Given these improvements and a volatile global marketplace, the equation for value creation and financial return for U.S. manufacturing is offering a better return.
Improving U.S. Manufacturing Capacity And Capability
Improving U.S. manufacturing capacity and capability requires more than investment in physical manufacturing space. Deploying a comprehensive operational strategy is needed to provide cost competitiveness and low risk. Operational strategy includes deployment of Current Good Manufacturing Practices (cGMP) with enhanced quality management systems (QMS) capable of supporting continuous manufacturing (CM), real-time monitoring, and efficient supply chain planning.
These techniques have been under development for some time between industry, academia and the FDA. Significant accomplishments in CM capabilities have been developed and certified by U.S. manufacturers including Eli Lilly, Phlow, Thermo Fisher, and CONTINUUS. Other American-based companies are in the process of investing, building and certifying continuous flow capabilities. A 2022 study by the University of Maryland found that deployment of CM processes for oral solid dosage formulations have “yielded higher NPVs than batch processes, even when accounting for conservative cost volatility scenarios. Additionally, investing in CM technology in the U.S. under current tax rates resulted in positive expected NPVs over batch technology investments in China or India for both brand and generic companies.”
In addition to deploying CM processes, the deployment of enhanced QMSs bringing together compliant processes and technology adds critical efficiency to quality and compliance. These tools allow for data collection, statistical trending, quality attribute monitoring and real-time process monitoring and release.
While several global pharmaceutical companies recently made public announcements to increase their investment in U.S. production capabilities, the construction and validation of these facilities will take years to complete. In the interim, strategic supply chain questions should be asked about the current paradigm focused on finished product. Finished goods often have a shorter shelf life than API and Key Starting Materials (KSM) and as a result, the storage of these materials in lieu of finished goods can reduce the risk of expired finished goods and financial write downs. Going forward, companies and government purchases for strategic stockpiling should consider the storage tradeoffs between finished goods and raw materials as a way to efficiently manage supply and costs.
Government Support
U.S. Government support to grow manufacturing spans three primary areas: corporate taxation, incentives (financial and regulatory), and trade/tariffs. Properly coordinating these three areas can provide long term incentives for ongoing U.S. and regional investment.
The TCJA of 2017 is set to expire at the end of 2025 and while some CEOs may be public in their comments, lobbyists are working with Congress to extend those and other incentives in the current tax bill under consideration. Lilly’s Chief Executive David Ricks recent statement in the Wall Street Journal sums up this sentiment: “We hadn’t built a new site in the U.S. in more than 40 years until the first set of Trump tax cuts, so we need to see those either extended or improved to support this.” Given the high cost to build and validate pharmaceutical facilities, large U.S. multinational companies like Lilly will always explore global tax and regulatory laws to determine locations.
In addition to broad based tax reform, the CARES Act of 2020 provided incentives for U.S. drug manufacturing. These included priority review of U.S.-produced drug applicants, manufacturing tax credits, and buy America requirements. While this legislation initiated support for U.S. manufacturing, important incentives related to priority drug review and tax credits have expired.
The U.S. Senate — through a 2022 Congress decree that charged the National Security Commission on emerging Biotechnology (NSCEB) with developing recommendations to advance U.S. biotechnology leadership — recently published an action plan. The report proposes a comprehensive set of recommendations for the Executive Branch, House of Representatives, and Senate to address the role of U.S. leadership in biotechnology development, manufacturing, and treatment. Some of the manufacturing recommendations include support of infrastructure development, workforce training, and simplifying regulations. Portions of these recommendations were included in the FY25 National Defense Authorization Act.
While corporate taxation, regulations, and incentives are well documented and transparent, the wild card is trade and tariff agreements. As of this writing, President Trump’s current tariffs are only on Chinese pharmaceutical materials. However, his threats of tariffs on other global pharmaceutical suppliers are still being finalized and expected to be announced in the near term.
Considering the current political environment, companies must understand the ongoing risks of U.S. tariffs in their planning process. Over the past eight years, both political parties valued tariff benefits to appeal to voters. While President Trump in his first term increased tariffs, President Biden continued enforcement on many goods including pharmaceutical materials from China during his term.
Collaboration Required
A robust supply chain which includes U.S. manufacturing capability and capacity will be more responsive and secure to the supply of essential medicines to patients and their doctors. The ongoing collaboration between industry, academia, regulators, and politicians will ensure innovation to maintain a cost competitive and low risk source of supply.
About The Author:
Dave Stowe is the Managing Partner at Adventus and supports clients’ strategic procurement and sourcing efforts to unlock supplier value and grow their business. We work with client teams to align their operating model across organizational buying responsibilities, policies, processes, systems and metrics.