Importance Of Quality Management On IT Projects Within The Pharmaceutical Industry
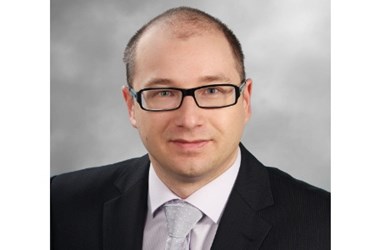
By Luka Mladinov, PMP
If asked, “What is quality on projects?” many people would answer, “When the customer is happy with the final result." To avoid such unclear criteria as “the customer is happy” we need to define more explicit quality requirements and acceptance criteria and determine how to measure the quality to ensure that predefined requirements are met. In terms of IT system’s implementation projects within the pharmaceutical industry, we could say that the quality or validation means establishing documented evidence, which provides a high degree of assurance that an individual application will consistently provide a product meeting its predetermined specifications and quality attributes. In shorter terms, the quality is defined as a degree to which the project fulfills requirements.
Executives may say, that they do not have time or money to spend on quality management in addition to regular project management costs, or that the internal procedures do not require quality management plans for system development projects. Such approach may result in higher number of project changes, rework and perhaps even some audit findings. The more changes and rework is required on the projects because of ill-defined quality requirements at the beginning, the more effort and resources may be required later. Even though by the definition, it is project manager’s job to ensure the project’s quality, the theory does not always fit in with the practice. In reality project managers, especially those with IT background, neglect to focus on relevant regulatory requirements, quality procedures, quality standards, documentation requirements, etc.
It certainly is a better and safer practice to plan quality in advance than hope that no quality gaps occur. And yet, pharmaceutical companies invest a lot in retrospective validation activities on already running systems.
Surely, more experienced project managers, especially those with PMP certification, understand the importance of quality management plans and are devoting a lot of attention to quality. Cases where IT projects within the regulated environment have been driven without sufficient quality management skills pose a risk not just to the receiving organization, but also to the users of company’s products and services. In today’s high-tech world, almost all stages of any product development life cycle are supported by different business, IT and production systems. If these systems are not properly validated during their implementation, there is no guarantee for their stability, safety and compliance with pre-defined specifications.
Although all systems are tested before they are put into operational use, not all system functions are equally critical. Therefore, a testing scope, approach and depth must be defined in quality plans and test plans during the system validation activities. In addition, critical systems have to be developed in accordance with required compliance controls, which, in many cases, are poorly addressed during requirements gathering process. If regulated controls are not properly defined and later on implemented within the scope of the design phase, a failure of system’s function could have a considerable business, compliance and even safety impact. It goes without saying that a failure of one critical function could lead to product delays, loss of sales, damage to environment or customer health, product recalls, warning letters or more serious regulatory penalties. Implementation and proper execution of quality management process brings measurable benefits to companies, such as:
• Better understanding of internal processes: information gathered through the quality management activities enable the companies better insight and control of internal business processes and supporting applications
• Higher efficiency of internal processes: in depth understanding of internal business processes give the companies an opportunity for their optimization which leads to increase in efficiency of internal teams and therefore lower operating costs
• Lower risk of defaults: by exercising quality management, companies can identify various risks within processes and projects which enable the definition of preventive actions in order to decrease the likelihood of product defaults
• Consistent high quality of products and services: by implementing and applying quality management procedures during the initiation, planning, execution, monitoring & controlling and closing project management process groups, companies can ensure consistent high quality of products and services
• Compliance: quality management enables companies proper identification, analysis and documentation of regulatory requirements and their implementation during the development phase which forms the basis for quality reviews and audits
• Customer satisfaction: quality management activities help create safe, reliable and qualitative products and services which always has a positive effect on customer satisfaction
• Prevention of tacit knowledge loss: proper documentation is critical to compliance because it enables good insight into the system workflows and ensures that the companies will not lose valuable system information in case of personal rotation. Furthermore, system documentation enables more efficient knowledge transfer and shortens the required training time of new system users
• Better system’s operations and maintenance: up-to-date system documentation helps IT teams during change management and configuration management activities.
Quality management is essential not only within the pharmaceutical industry related projects. It is also required within other regulated industries, where safety and health of the consumer is dependent on the quality of products and services that these companies are providing. Paying attention to and understanding of quality management contributes to remediation of many issues that can arise within the projects and to ensuring compliance with increasing regulatory demands.
About The Author:
Luka Mladinov, PMP is a Senior Consultant working at Liance GmbH, a consulting company based in Switzerland which provides quality, compliance and service management services for global life science and pharmaceutical companies. In 2011 he was a member of the executive committee at PMI Slovenia Chapter. He can be reached at luka.mladinov@liance.ch