Recent FDA Inspections In India Indicate New Focus On Tablet Press Operations
By Fred A. Rowley, Solid Dosage Training
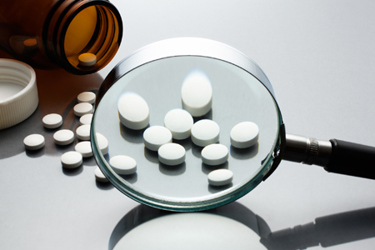
Shortly before Covid hit the world in early 2020, the FDA investigators in India began to shift their focus away from laboratory and data manipulation and toward a closer look at tablet press operations. Following emergence from the Covid epidemic in 2022, the FDA resumed inspections of the Indian-based generic industry at an accelerated rate that continues through today. A high percentage of observations continue to focus on tablet press operation. Specifically, the new interest centers on the critical process parameters (CPPs) and on the automatic weight control (AWC) system and the establishment, validation, and verification of the minimum/maximum tablet weights specified on the individual product batch records. At least five different firms have been either cited with a form 483 or given a warning letter concerning substandard procedures used to assure the public that out of specification tablets are removed from the batch.1-5
At the heart of the AWC-based control system is a value defined as the “compressing force” used to manufacture a tablet.6 Using the compressing force required to manufacture a tablet having the target weight, both the minimum and maximum tablet weights specified in the batch record can be established and verified, thereby assuring that tablets out of weight specification will be eliminated from the batch.
In addition to the AWC, the language used by the agency in communications (483s/warning letters) indicates that other critical processing parameters are also either inadequate or absent from the information gathered and attached as part of the overall batch documentation.
Many companies have had to face this unexpected development and have scrambled to update their process validation to include these other CPPs. The question at hand then becomes what are these critical operating parameters that we should include in our expanded validation effort? I briefly describe these generally accepted parameters in Table 1below.
Table 1: The Generally Accepted CPPs For The Modern Tablet Press.
- Fill volume: weight
Compressing Force* (on most presses) - AWC min/max weight limit settings
- Pre-compression thickness
- Main or final thickness
- Pre-compression punch entry
- Final compression punch entry
- Powder hopper:
Height (old presses)
Position of a slide gate or valve above the powder hopper - Feeder speed
- Turret speed
- The punch protection (overload) system
*Many companies do not view compressing force as a true CPP. Rather, it is viewed as a product of the actual fill volume and thickness setting at a specific turret speed.
Of these 10 parameters, many generic pharmaceutical companies in India appear to have neglected the pre-compression settings, the valve (or lack of valve) above the feeder used to control the powder flow, and the overload set point that is used to protect both the operator and the punches used to manufacture the tablets. In fact, some of these critical CPPs are neither recognized nor identified on the individual product master batch record. And finally, many companies allow the operator to set these machine set points without documenting them as part of the batch history. This then relies on the level of training and press understanding that any individual tablet press operator has rather than the application of good press operating science as the basis for making individual product set points. Further, since the set points used are frequently not recorded on the batch record, there is no ability to verify that these controls were used correctly in the event of a problem.
Any investigation generated for out of specification (OOS) results for physical attributes such as tablet hardness, content uniformity, capping, lamination, and weight variation must include a review of these settings and any changes made during batch production. And a brief review of the cited form 483s and warning letters from the FDA indicates that certain CPPs are not sufficiently addressed.
Some firms have demonstrated resistance to the FDA position that certain controls may be critical for certain products while less important for others. For example, if a particular blend tends to entrap air after final blending, then the pre-compression punch entry as well as tablet thickness controls become critical in preventing “capping.” For blends that percolate air immediately after final blending, the same controls become much less important.
Again, the FDA issued an observation on a form 483 given to KV Pharma in March 2006 concerning the control and documentation for the maximum tip pressure for punches, yet very few companies have a formal system for such documentation.7 Exceeding the maximum pressure the punch tips can withstand may result with broken pieces of the tip in finished tablets. At least four recalls of pharmaceutical tablets have occurred in the U.S. within the past 36 months for suspected pieces of metal tips embedded in the tablets.
Finally, the FDA has indicated through current language seen in various form 483s and warning letters issued to generic companies that the agency holds the company using tablet presses responsible for understanding, validating, and maintaining current the relevant machine settings for these and other critical operating set points regardless if the press manufacturer did not engineer its tablet press with these controls.
Tablet press manufacturers are also being forced to recognize design flaws in the powder flow systems used on their machines, inadequate descriptions of critical machine controls, and in some cases the absence of effective punch protection systems. These deficiencies leave generic companies with limited options when facing agency concerns about process control.
Going forward, it may benefit a company to review its approach to tablet press operation in view of these new developments and enhance its validation system to identify, validate, and document these critical settings.
References
- Indoco Remedies, Warning letter, July 2020.
- Aurobindo Pharma Ltd, Form 483, May 2022.
- Zydus, Form 483, May 2019
- Glenmark, Form 483, May 2022 and Warning Letter, November 2022
- Sun Pharma, Form 483, August 2022.
- F. A. Rowley: “Compressing Force: Myth Vs Reality”, Pharmaceutical Manufacturing magazine, 7: 1, 28-33, 2008.
- Form 483 given to KV Pharma in March, 2006 states: “The master and batch production records have not been revised to specify the tooling rating and to require documenting the compression force.”
About The Author:
Fred A. Rowley has more than 40 years’ experience in the pharmaceutical and nutritional supplement industries in manufacturing, technical services, and R&D settings, with particular expertise in solid dosage manufacturing and training. He has knowledge of the granulating, blending, tablet compressing, and film coating processes for more than 800 API drug substances. He is and has been retained as a subject expert by law firms, equipment manufacturers, international pharmaceutical and nutritional supplement companies, and compounding pharmacies, and has lectured at the FDA, the ISPE, and at many colleges of pharmacy around the world. Previously, he has been director, manufacturing technical support, for Watson Laboratories; plant manager, tablets and capsules, Weider Nutrition International; vice president, operations, Arnet Pharmaceuticals; OROS operations manager, Alza Corporation; and bulk solids manager, Syntex FP, Puerto Rico.