4 Ways To Gain A Competitive Edge In This Bio/Pharma Talent Shortage
By Michael Goldberg, vice president of strategic partnerships, Harvey Nash USA
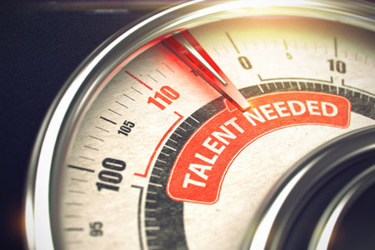
It’s no secret that finding manufacturing talent is incredibly challenging and the lack of workers is having a negative impact on productivity and growth. A 2021 study from Deloitte and the Manufacturing Institute estimated that the manufacturing skills gap — which is now anticipated to leave 2.1 million jobs unfilled by 2030 — could cost the U.S. economy as much as $1 trillion.1 Like other industries, manufacturing has been impacted by historically low unemployment rates, but it also has other challenges including a retiring workforce, misperceptions about the industry, and the need for in-person work.
It can be even harder for pharmaceutical manufacturing companies to recruit employees, especially for technology and engineering roles. For one, candidates need to understand the industry's complex technical, regulatory, compliance, and quality control requirements, including the Drug Supply Chain Security Act. In addition, experts point to the fact that “manufacturing of cell and gene therapies requires new technologies and processes and, therefore, highly skilled and specialized knowledge.”2
Unfortunately, insufficient industry-wide investment in employee training and development programs has limited the accessibility to suitable candidates, especially in key positions such as process engineers, quality assurance specialists, manufacturing system analysts, and automation engineers. To overcome these challenges, pharmaceutical companies should prioritize gaining control over the talent management process in order to build a robust candidate pipeline. Here are four effective strategies for recruiting, training, educating, and retaining workers.
1. Embrace Strategic Workforce Planning
The discipline of workforce planning helps organizations understand their current skill shortages and predict future needs to improve recruitment efficiency and prepare for long-term talent development. This is especially critical with the rapid rise of automation and technologies like generative AI, which can greatly streamline the manufacturing process but requires new skills. In its study on pharma operations, McKinsey estimates that 50% of existing work activities in the pharmaceutical and medical manufacturing industry could be automated.3
This shift will require planning that few companies have fully undertaken. And while each may have a different approach to workforce planning, there are a few important steps to consider:
- Conduct a talent needs assessment of the existing workforce to understand skills gaps and identify potential employees for upskilling programs.
- Survey employees to gather feedback on their current roles, interest in learning new skills, and where they see an opportunity to improve internal operations.
- Conduct research and network with industry peers to gain a wider understanding of not only industry trends and new technologies but different ways to recruit and train for evolving manufacturing roles.
- Predict future needs and determine how to recruit specifically for candidates with either the right skills for those positions or those who are life-long learners willing to take on new challenges.
- Include compliance planning in the process to ensure there are enough employees that understand regulatory and safety requirements.
Teams that are new to workforce planning should keep in mind that these tasks are not meant to be accomplished overnight. However, a critical first step is to conduct the talent needs assessment. The other tasks can be spaced out as long as timelines are established so they are not pushed to the back burner.
2. Build Partnerships To Grow The STEM Workforce
A McKinsey study found that the pharmaceutical industry has been slow to address the tech skills gap and that disruptors such as analytics and digitization have exacerbated the problem in more than 80% of pharma manufacturing companies.3 To help bridge the divide, most companies are eager to provide training but too often rely on overwhelmed managers to coordinate a program.
Instead, organizations should try to dedicate an employee to focus solely on building and managing an upskilling and reskilling program. This position would likely be filled by a human resources (HR) professional who has expertise in identifying skill gaps, organizing development programs, and aligning these efforts with the overall organizational strategy. In addition, the success of such a program may require collaboration with technical departments, especially when it comes to specialized skills in pharmaceutical manufacturing.
A dedicated resource can take the time needed to identify outside training providers and online programs that offer the best courses for the skills needed now and those needed for future roles. Even more importantly, they can establish strong connections with academic institutions to gain access to an ongoing supply of graduates and allow for continuous upskilling opportunities for existing employees. These can be universities that have specific four-year programs in bioengineering, biomedical engineering, and pharma sciences or any academic institution that graduates students with skills in STEM fields.
Experts agree that building the workforce of the future will require these types of innovative partnerships to grow the tech talent pipeline. In fact, the Pharmaceutical Research and Manufacturers of America (PhRMA) and TEConomy Partners found that “biopharmaceutical companies are leveraging educational partnerships across dozens of U.S. institutions to prepare students for specific careers within the industry and utilizing a range of partnerships to develop specific workforce skills.”4 The report includes a wide range of corporate/academic partnerships that focus on curriculum and program development; internships, fellowships and mentorships; access to facilities and equipment; and customized job training programs. For example, the Wake Technical Community College in North Carolina provides certificates and associate degrees for employment in pharmaceutical manufacturing and related industries and the Worcester Polytechnic Institute in Massachusetts, in partnership with the biotechnology and biopharmaceutical industry, provides customized workforce training.
3. Use A Data-Driven Recruiting Strategy
Pharmaceutical manufacturing has experienced a great deal of change as the demand for injectables and customized medicines continues to grow, impacting production, packaging, logistics, and more. Additionally, the move from Industry 4.0 to 5.0 and greater use of automation technologies, data analysis, and cybersecurity tools means the required roles are rapidly evolving.
Hiring for these advanced tech positions requires tapping into data-driven recruiting approaches to uncover key trends, improve the caliber of hires, reduce hiring timelines, predict future workforce needs, and optimize overall recruitment efficacy. Some examples of how recruiters can leverage AI and data analytics tools include:
- Skillset Evaluation: Pinpoint common skillsets and qualifications that are most prevalent in successful employees serving in specialized roles such as bioprocess engineers, quality assurance analysts, or clinical data managers. This can guide recruiters to target candidates with the same training and experiences.
- Transferable Skills Analysis: Identify related fields that deliver candidates who successfully transitioned into pharmaceutical manufacturing roles. For instance, candidates who have a background in biomedical engineering or software development might adjust well.
- Educational Background Review: Look at patterns in education that have led to successful hires in the past. Certain universities, courses, or degrees might consistently produce candidates who excel in pharmaceutical manufacturing roles.
- Retention Study: Analyze the characteristics of employees who have had high retention rates and success in specific roles within the organization.
- Geography Assessment: Gain an understanding of where potential candidates are geographically located to help increase the talent pool. For instance, in 2022, the Bureau of Labor Statistics found that Puerto Rico was tops in candidates in pharmaceutical and medicine manufacturing exports, followed by Indiana, North Carolina, California, Illinois, and Pennsylvania.5
- Social Media Behavior Check: Study how candidates engage with industry-related content online to identify those who are actively keeping up with trends, new technologies, and regulatory changes.
4. Employ A Mix Of Talent
Increasingly, pharmaceutical companies are augmenting full-time manufacturing positions with contingent workers that allow them to scale production up or down in response to market demand and economic conditions. Additionally, the adoption of continuous manufacturing in the pharmaceutical industry is likely to require a more flexible workforce that can be available around the clock and help adhere to quality and safety demands.
One challenge with hiring contingent and temporary workers is maintaining visibility. It’s easier to manage full-time workers who are directly employed by the company. However, contingent workers are typically hired and managed by an outside organization. Workforce management systems can help track contingent workers as well as optimize scheduling, ensure regulatory compliance, lower labor costs, and forecast labor needs. Some features to look for when choosing a workforce management system include:
- Regulatory Compliance: This helps companies adhere to FDA regulations, and other industry-specific standards, to avoid violations and penalties.
- Integration Capabilities: The system should easily integrate with existing HR and production tools to better align both contingent and full-time worker data within a unified platform.
- Real-Time Visibility: These insights can track hours, skills, certifications, and performance metrics in order to provide visibility into the entire workforce.
- Data Security and Privacy: It’s vital that the system adheres to high security standards that protect employee data and any proprietary information related to production processes.
- Analytics and Reporting: These features can provide valuable insight into labor trends, cost analysis, and workforce efficiency.
- User-Friendliness: A system that is intuitive and easy to use will facilitate faster adoption rates for managers and employees.
- Vendor Expertise: Vendors with a proven track record in the pharmaceutical industry are more likely to understand the unique needs and considerations of the field.
When it comes to balancing full-time and contingent workers it’s also important to recognize that some roles are better suited for a particular type of worker classification. For instance, full-time employees typically fill positions that require complete integration into teams or are core to the business, while contingent workers often take on project-based roles or those that require specialized, sought-after skills.
The Future Of Pharmaceutical Manufacturing Is Now
While the pharmaceutical industry may have been initially slow to accept the technology revolution, it’s increasingly clear that the writing is on the wall. Many organizations are now willing to consider sweeping changes that allow them to capitalize on the promises of advanced technology, digital solutions, data analysis, and more. However, unless the entire industry commits to preparing the workforce for this transformation, it will be virtually impossible for any organization to benefit from these advances, ultimately negatively impacting the very people they’re committed to serve – patients.
References
- U.S. Manufacturing Skills Gap Could Leave As Many As 2.1 Million Jobs Unfilled By 2030, Deloitte and The Manufacturing Institute Study Finds. https://www.prnewswire.com/news-releases/us-manufacturing-skills-gap-could-leave-as-many-as-2-1-million-jobs-unfilled-by-2030--deloitte-and-the-manufacturing-institute-study-finds-301281967.html
- 2023 Pharmaceutical Manufacturing Trends, Clarkston Consulting. https://clarkstonconsulting.com/insights/2023-pharmaceutical-manufacturing-trends/
- Pharma operations: Creating the workforce of the future, McKinsey & Company. https://www.mckinsey.com/~/media/McKinsey/Industries/Pharmaceuticals%20and%20Medical
%20Products/Our%20Insights/Pharma%20operations%20Creating%20the%20workforce%20of
%20the%20future/Pharma-operations-Creating-the-workforce-of-the-future.pdf - Enhancing Today’s STEM Workforce to Ensure Tomorrow’s New Medicines, The Pharmaceutical Research and Manufacturers of America (PhRMA) and TEConomy Partners, LLC https://phrma.org/-/media/Project/PhRMA/PhRMA-Org/PhRMA-Org/PDF/S-U/TEConomy-PhRMA-STEM-Report-Final.pdf.
- Top 6 States and Territories in Pharmaceutical and Medicine Manufacturing Exports, Bureau of Labor Statistics. https://www.bls.gov/mxp/publications/regional-publications/charts/top-6-pharmaceutical.htm
About The Author:
Michael Goldberg is vice president, strategic partnerships, at Harvey Nash USA. You can connect with him on LinkedIn.