What Will Have A Big Impact On Your Biopharma Manufacturing Organizations?

By Rob Wright, Chief Editor, Life Science Leader
Follow Me On Twitter @RfwrightLSL
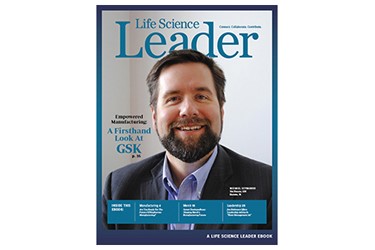
When putting together the manufacturing outlook article for our December 2017 issue, we encountered a good problem to have — more content than could possibly be squeezed into the printed pages of Life Science Leader magazine. Such challenges sometimes occur when fortunate enough to have 10 biopharmaceutical key opinion leaders eager to share their industry insights. Such predicaments are one of the reasons we created our exclusive Beyond The Printed Page online section of the magazine. We hope you enjoy this most recent installment with four biopharma manufacturing executives disclosing what is being done at their organizations to impact manufacturing operations in 2018 and beyond. If you like what you read, please consider becoming a subscriber today at our current special rate of $49 (enter coupon code ED49). For while Beyond The Printed Page remains free, accessing all the great content Life Science Leader magazine has to offer requires a subscription. By the way, in case you missed it, here is a link to some additional manufacturing thought leadership — How Might Biopharma Manufacturing Differ In The Next Decade?
What Are You Doing That Will Have A Big Impact On Your Manufacturing Organization In 2018 And Beyond?
Wolfram Carius, Ph.D., head of pharmaceuticals product supply, Bayer: Our activities to benefit or spearhead developments in our organization are as follows. First and foremost, it is imperative to have a continuum between the technical development and technical operations organizations along the product end-to-end from drug substance to drug product and device. An active technology radar, evaluation and piloting of external and internal innovation are essential to stay up to date, but need to be based on a clear strategy for where we do and do not focus, where we will and will not partner or invest, and building on a few key technology platforms. Concrete examples include involvement in CRISPR-Cas9, continuous manufacturing for new chemical and new biologic entities, digitalization pilots, segmentation in supply chain and manufacturing or realizing new modular factory concepts. Ultimately however, it is all about attracting, developing, and retaining the right talent.
Philippe Luscan, EVP global industrial affairs, Sanofi: At Sanofi we have made a significant investment of €4.7 billion [$5.6 billion] over the last five years to expand our capacity and scale. We are also looking at digitizing our supply chain, from which we will gain end-to-end visibility to better manage inventories and forecasts. We are also embracing the Internet of Things (IoT) approach to manufacturing, particularly in regards to implementing a new generation of sensors able to collect a wider set of data points at reduced costs. This technology is empowering Sanofi to move away from the traditional model where data at our sites for quality, production, and maintenance are stored in silos, and towards a more integrated model where information streams are combined into a single data point. This new, digitally-enabled approach to data management makes it easier to gain powerful insights into the performance of Sanofi sites.
Paul McKenzie, Ph.D., EVP pharmaceutical operations & technology, Biogen: Development of our scientific and manufacturing personnel is critical for our long-term success. The introduction of recipe-based execution, real-time analytics and predictive models in-line, at-line and in laboratories will require a fundamentally different skillset to ensure safety, quality and reliability of our operations. Work will move from execution of many activities to analyzing data, understanding models and predicting next steps. This move from being “busy-busy” with tasks to analytical thinking and real-time response will require a significant cross-training across current functions, and will challenge the curriculums of universities supplying new talent to our industry.
Chhaya Shah, SVP manufacturing & technical operations, Synergy Pharmaceuticals: The biggest impact that we have already made and will continue to refine is having a talented pool of employees that are driven to operational excellence (OPEX) thinking, with a common goal of providing products with the best quality and value for our customers. Being in an outsourced manufacturing model, it is essential that our organization thinks in terms of problem-solving and ongoing improvements of our processes internally, and ensuring that this mentality is transferred and embedded in our contract manufacturing organizations. This process involves strategic partnership with our manufacturers to educate and provide as much information about our customers’ needs as possible. Keeping a mindset of OPEX in our organization will transcend to our partners and keep employees empowered, focused on continuous improvement, and will ultimately bring value to our customers.