Why Drugs Cost So Much

By Rob Wright, Chief Editor, Life Science Leader
Follow Me On Twitter @RfwrightLSL
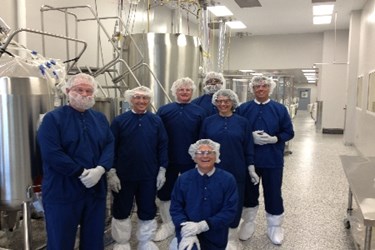
By Rob Wright
I recently had the opportunity to tour a biopharma manufacturing facility in St. Louis. It served as a great reminder as to the stringent requirements which go into creating a safe drug supply. It also explains why some drugs cost so much. When people learn I work in the pharmaceutical industry, I often get questioned about the price difference between generic and branded drugs. Sometimes I am asked for my opinion on “all-natural” supplements. I am always sure to point out how marijuana and other drugs are “all-natural” and thus, not necessarily good for you. Another complaint I hear revolves around the price of drugs and devices as being too expensive. I wish the general public and government legislators could take a similar tour to gain a deeper understanding of what is involved in the drug manufacturing process. Consider this a virtual tour of some aspects, so you can understand some of the processes these manufacturing people go through every day to make life-saving and safe treatments for your friends and family, and why drugs cost what they do.
Gowning In
When biopharmaceutical manufacturing workers show up to work, one of the first things they do is go to a locker room. Here they pick up a pair of scrubs which are sealed in plastic. The process of putting these on is referred to as “gowning in.” The manufacturing employees put these on, being sure to not allow the pant legs to touch the floor. The pant legs have gathered cuffs around the bottom to keep them from dragging on the floor. The scrubs top is long sleeved with cuffs as well, and three snap buttons which need to be buttoned all the way up to the collar. While I was gowning in, I thought back to recent experiences in healthcare settings, such as physicians wearing the same scrubs for multiple surgeries. Having worked in a hospital, I recall scrubs being washed, folded, and stored by size, but not being stored in sealed plastic. Hospital scrubs are short sleeved, and don’t have gathered arms or legs. Next time when you see a clinician walking back and forth between the hospital and their office, see if their pant legs drag on the ground. What type of bacteria might they have picked up along the way? I wonder.
After putting on the manufacturing scrubs, we wash our hands, and then head into a separate room. Here we put on hair and beard nets. On your way through the doorway, you will note there are tacky floor mats which pick up dirt from your shoes. Next, you sit on a bench which straddles parallel red line on the floor, denoting the side where you must have shoe covers on to walk. Here, you put on shoe covers which go half way up your leg and then tie. The trick is to sit on the bench in such a way that you can put on the boot of one leg, and without having it touch the floor, swing your leg over so as to have the covered foot on the side of the red line where shoe covers are required. Then you repeat the process with your other leg. You will now move into another room, through a door to put on gloves. By the way, if you like to chew gum, sorry this is not allowed, and you will be asked to remove it.
Next come the gloves. When you put these on, your gloved hands are then sprayed with a solution, front and back, and you are instructed to rub your hands together. Don’t forget the safety glasses. You are now able to enter a non-sterile manufacturing process. For sterile manufacturing, it is even more involved. When you go on your lunch break, you have to go through the same process, with an entirely new set of scrubs, hair nets, and so on. Think about how many times you might go to the restroom during a typical eight hour day. These employees work in 12-hour shifts. If they need to use the restroom, they have to go through the complete gowning in process each time. I would imagine these workers are careful about their coffee consumption so as to minimize the need to run to the restroom. I would imagine there are very few smokers in this manufacturing facility. Can the same be said for your local hospital?
Not Just Clean But ISO Clean
Now that you are all gowned in, you can enter the work space. As you walk through the halls you will notice how clean everything is. You could eat off this floor, but no snacking allowed in this space. The term ISO gets thrown around a lot, which stands for the international standards organization and is being referenced for cleanroom manufacturing standards. ISO cleanroom classifications are rated according to how much particulate of specific sizes exist per cubic meter. Here is a useful chart which shows the classes and how many particles of 0.1 microns up to 0.5 microns are allowed per cubic meter. Typical ranges in the areas I was in ranged from 6 to 7, though I saw a special booth the facility had to install to satisfy the Turkish Ministry of Health (MOH), which created a space of ISO 7 within an ISO 8 room - which was satisfactory to all of the other regulatory agencies (i.e. EMA, FDA) which toured the site. Yet because MOH believed the booth was necessary, the company invested $30,000 to satisfy just one agency. One more reason drugs cost so much. Turkey, which has the smallest population of all the countries whose agencies toured and approved the Gallus BioPharmaceutical site, demonstrate how the lack of regulatory harmonization results in companies, if wanting to do business globally, having to manufacture to the highest regulatory standard.
The next time you are wondering why drugs cost so much, consider this — your drug, unless ordered from some online pharmacy with a dubious reputation, is probably manufactured in a facility that is not only significantly cleaner than your local hospital, but by people who don’t require a bathroom mirror reminder sticker telling them all employees must wash their hands before returning to work. All of these precautions come with a cost and contribute to the price of a drug, and I am not including the costs of the manufacturing equipment, electricity, salaries of employees, and all of the other components necessary to produce a safe biologic. Consider this the next time you post on Facebook how expensive your prescription drugs are.