Novartis And The Arrival Of The Continuous Manufacturing Facility

By Louis Garguilo, Chief Editor, Outsourced Pharma
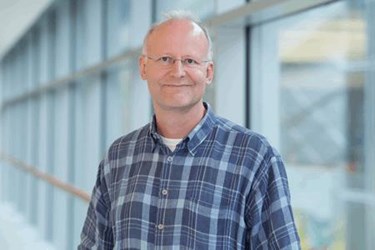
Our dogged determination to answer this question – How can the industry introduce disruptive innovation and technologies into drug development and manufacturing? – recently led us to the Novartis-MIT Center for Continuous Manufacturing (documented in this article.) That in turn propelled us to Basel, and the doorstep of Markus Krumme, head of continuous manufacturing for Novartis. Here, at the new Novartis Continuous Manufacturing Facility, we’re finding more answers.
Interestingly, those answers – albeit with intriguing twists – form an already well-known blueprint for innovation. Krumme shares this with us, and while doing so imparts valuable insight into continuous manufacturing, a disruptive innovation the likes of which are rarely seen in our industry.
Crazy C-Suites And Colleges
First, those twists. The initial pursuer of disruption isn’t a rouge entrepreneur with mythical beginnings in a garage or small lab. In fact, he sat at the top of a very big and famous pharmaceutical company.
According to Krumme, the narrative starts in 2005 with a single question on a slide presented to Novartis drug development and manufacturing executives. “Why don’t we have facilities that can continuously produce materials?” then-CEO Daniel Vasella asked.
“I remember at the time asking the head of manufacturing what he thought,” says Krumme. “He said it’s a rather crazy idea; he’d ‘wait and see.’ Four weeks later when Vasella asked again, this high-caliber manufacturing head with responsibility for thousands of people, now said, ‘Well, obviously this isn’t going away. I need to do something.’ That was literally the start.”
A working group was pulled together to form a scientific and technical perspective. The group focused less on implementing minor innovations or refinements, but squarely on an investigation of a full-blown paradigm change. “We asked: ‘If you want to do something completely different, where do you go for help? Do we go to a research setting where they know and teach the current industry standards and theoretical background? Or to somebody known for trying some crazy things.’
“So did we go to MIT because they were the most capable in the field? No, we went because they had a reputation for thinking outside the box. We intentionally went to a research setting that had bright minds, but was not biased by the industry. That’s how we ended up at MIT.”
Thus, the spark for innovation came directly from the C-Suite of a global pharmaceutical, but the fire would be stoked at a university setting. Our second twist of sorts is how Novartis initiated “an unusually long-term and open strategy” with MIT, extending ten years. Krumme describes the initial assignment for this industry-university collaboration:
“We came up with a significant amount of money to create the Center. We simply stated our vision: Do something in the area of continuous manufacturing for pharmaceuticals. Do it with bold strokes. We want disruptive innovation. We won’t tell you what our specific development goals are. You dream up something with just two constraints: it needs to be applicable to the chemical field of manufacturing, and it also needs to be fully applicable to pharmaceuticals. Then we left them alone for a couple of years.”
When Novartis returned to “see what we could harvest,” they found enough to begin implementation of new technology back home in Basel.
The Rise Of A Continuous Manufacturing Facility
Krumme was responsible for implementation of the new learning. The original idea had been to create a Technikum, a technical development facility used for experimenting with new ideas and equipment. That got upgraded quickly to a pilot facility, and when all was said and done, Krumme and team had in fact designed a cGMP-compliant facility to produce and supply clinical-trial materials, and potentially material for commercial launch. The Continuous Manufacturing Facility started as “a building shell with the insides completely gutted,” and now includes approximately 3,200 square feet of cGMP space and all newly designed equipment.
“The MIT collaboration significantly influenced our thinking and the facility, but then we predominantly relied on further developed at Novartis. We’d created a think tank, if you like, that came up with new ideas and concepts that were de-risked and demonstrated. We call that ‘the redline,’ and we published the first end-to-end continuous process as a result. At that point, we felt brave enough to take it to the next levels, and with a substantial internal effort and investment, we designed the process and facility.”
Share The Learning – Including with CMOs
In our precursor, we mentioned Novartis has allowed this new technology to be out-licensed. I ask Krumme: “Did Novartis consciously make the decision to spread what you’ve learned through the industry?”
There’s no hesitation in reply: “Absolutely,” he says. “That was a strategic goal behind a lot of this. We retain rights to the technology, but are not blocking others. Quite the opposite, we were open from the beginning in what we were doing at MIT. We’d like the entire pharmaceutical world to make this leap forward. Even a multinational of our caliber cannot do this alone.”
He continues: “Our industry is so highly regulated, we need coordination from many others. That includes from the outsourcing perspective. We are creating an open network of people and partners to join the journey. What was possible for us was to seed finance and develop, in order to create a substantial foundation for assuming the lead for a more widespread implementation. We want others not only to follow, but to act in the same way. That is a critical element for the adoption of disruptive innovation.”
Krumme circles us back to the main theme of our first article. “Continuous manufacturing isn’t a single technology,” he iterates. “It’s many enabling technologies. A practical example is a process we have at Novartis, with 20-plus individual steps. With continuous manufacturing, they all connect into one contiguous chain. That chain only works perfectly, though, if you have a solution for each step. Even a single step without a solution puts up a roadblock. You might figure out how to circumvent, but it stands in the way of creating a fully elegant, and from a quality and commercial perspective, attractive process.”
C-suite foresight; a long-term university-industry partnership for open innovation; initial investments from pharma; sharing the innovation industrywide; we’ve found these and other points on the blueprint of disruptive innovation. In the final part of our discussion with Krumme, we’ll dig deeper into the subject of quality in continuous manufacturing, as well as equipment and process development, and some closing thoughts.